Proceedings Vol. 30 (2024)
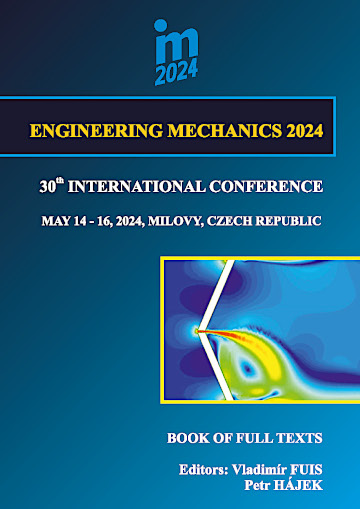
ENGINEERING MECHANICS 2024
May 14 – 16, 2024, Milovy, Czech Republic
Copyright © 2024 Brno University of Technology, Institute of Solid Mechanics, Mechatronics and Biomechanics, Brno
ISSN 1805-8248 (printed)
ISSN 1805-8256 (electronic)
list of papers scientific commitee
pages 142 - 145, full text

Laser shock peening (LSP) is a modern alternative to standard peening processes such as shot peening. In general, peening is used to improve the strength and fatigue resistance of components by hardening their surface. In LSP, a laser-induced shockwave is used to harden the material to a depth of the order of 1 mm, that is, roughly twice as deep as can be achieved with shot peening. Frameworks for LSP simulation have been developed since the end of the 1990s and are exclusively based on the finite element method (FEM). The critical component of the framework is the dynamic simulation of the elastoplastic shockwave that subjects the component material to a strain rate of the order 10−7 s−1 . In this contribution, we present a simulation framework for LSP based on the finite volume method (FVM) that allows for modeling the strain-rate hardening of the material. The framework is used to simulate the LSP of the 7050 aluminum alloy. Using a comparison of our FVM results with the FEM data available in the literature, we found that FVM can be applied to LSP simulation with the same success as the more traditional FEM.
back to list of papers
Text and facts may be copied and used freely, but credit should be given to these Proceedings.
All papers were reviewed by members of the scientific committee.